Keynote Speaker
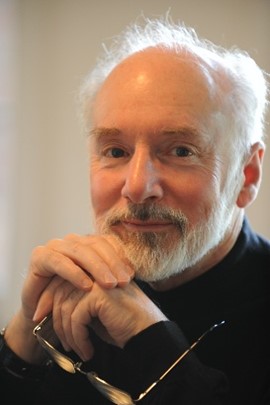
John Campbell
School of Metallurgy and Materials, Faculty of Engineering, The University of Birmingham UKSpeech Title: The Origin of Fracture
Abstract: Over recent decades it has become clear that the pouring of liquid metals is damaging to the liquid. The surface oxide is folded in, making a double oxide film, which acts as a crack. Most of our cast metals (but with interesting exceptions) are full of bifilm cracks originating from the casting process. The bifilm population, as a pre-existing population of cracks, is not easily detected because they are generally closed cracks with nano scale thickness. They are shown to initiate simple tensile failure, and fatigue. The bifilms become open cracks by the mechanism of precipitation cleavage, in which precipitates grown during certain sensitizing heat treatments form on the bifilms to reduce their strain energy of formation, and thereby prize the bifilms open. In this way metals become vulnerable to invasive corrosion, leading to stress corrosion cracking and/or hydrogen embrittlement. The reduction or elimination of bifilm populations by improved casting technology appears to lead to an order of magnitude increase in toughness of Al alloys and stainless steels, and appears to be a low cost technique to eliminate invasive corrosion, stress corrosion cracking and hydrogen embrittlement.
Biography: Educated in England at the universities of Cambridge, Sheffield and Birmingham he first trained as a physicist, then became a metallurgical engineer, but finally has spent much of his life in industry.
In the 1980s he built the casting operation for Cosworth Engineering, developing the Cosworth Casting Process, then a novel process making Al alloy cylinder heads and blocks for the Formula One racing engines, using counter-gravity filling of moulds by electromagnetic pump. The process has been taken up by Ford, Nemak and General Motors for the production of automotive cylinder blocks in North America and Mexico. This process still has the world record for production rates of sound and strong V6 and V8 blocks.
His industrial experience and his academic background including two masters degrees and two doctorates fitted him for his 15 years as Professor of Casting Technology in the University of Birmingham, UK. Here, he was able for the first time to define the nature of turbulence and the mechanism for the generation of casting defects, introducing the concepts of entrainment and the concept of the bifilm and the crack population of liquid metals. He has subsequently devoted much effort to the development of casting techniques to control defect formation. His mantra is the phrase “Making metals we can trust.”
He is currently working on the building of an integrated melting and casting machine which takes in tonnage quantities of recycled aluminium at one end, which is treated, producing aerospace quality aluminium castings and other high purity products with high properties at the other end. The process is low cost, high productivity, low labour content, low energy, low floor space, with few moving parts for maximum reliability. His other current interest is his quest to warn the world of the dangers of using vacuum arc remelted metals. It is not widely known that this expensive material contains bifilm cracks which bring down aircraft, but could be improved by abandoning the vacuum induction melted and cast electrode, and substituting a carefully cast low-cost air-melted electrode using the newly established casting technology.
His book “Complete Casting Handbook” published in 2011 and revised in 2015 is not light bed-time reading, but is all there: a bargain for the determined and fearless reader with an open mind. The “Mini Casting Handbook” 2017 and expanded in 2018 and 2023 is a basic, slimmed text specifically written for casting personnel.
His latest book “The Mechanisms of Metallurgical Failure - The Origin of Fracture.” 2020 is regrettably revolutionary and will be burned in the streets. It describes the potential elimination of failure mechanisms such as cracking, creep, fatigue, stress corrosion cracking etc in most metals, especially steels and high temperature alloys, by eliminating bifilms – the failure initiation sites introduced by turbulent pouring of the liquid.
In 1991 he was invited to become a Fellow of the Royal Academy of Engineering, and in 1993, Her Majesty, Queen Elizabeth, awarded him the Civil Honour, the Order of the British Empire, for services to casting technology.